In this section:
Periodic damage associated with vehicle dynamics
Periodic or quasi-periodic variations sometimes exist on rails with a wavelength of about 10-30m. Where this occurs, it is almost always the result of vehicle dynamic behaviour. Wear, plastic flow and rolling contact fatigue are often all periodic.
Straight track
The most common periodic or quasi-periodic rail damage in straight track is a result of vehicle “hunting”. When this occurs, wheelsets and the vehicle oscillate from side-to-side in a very periodic manner. Where there is flange contact the rail appears almost identical to a high rail, with gauge face wear and RCF on the gauge corner. The opposite rail appears like a low rail, with a flattened profile. Half a cycle further along (5-15m typically), the rail that appeared like a high rail appears like a low rail, and vice versa.
There are several reasons that “hunting” appears in localised areas. The most common reasons are tight gauge and profiles that have worn to conform too closely to the wheels. These increase the “effective conicity” and reduce the vehicles’ “critical speed”. Trains hunted on the rails shown in Section 1.1 immediately after these were transposed because of the increase in conicity from running in the root of the wheel flange.
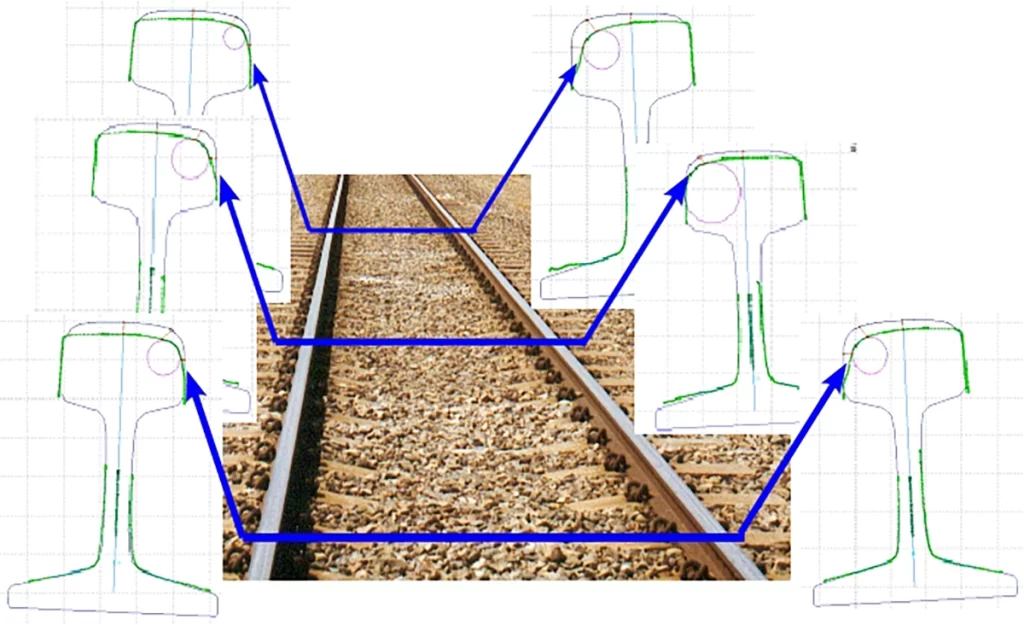
When a periodic pattern of such long wavelength becomes established in the rail, it is impossible to remove with current rail reprofiling techniques. Reprofiling can, however, be undertaken to reduce conicity, eliminate hunting and allow trains to run on the periodically worn rail.
Hunting is potentially a dangerous condition: apart from damaging rails, it can move the whole track laterally.
Curved track
Periodic damage can occur in curved track, where it is superposed on the damage that would usually be seen in a curve. The most obvious result is periodically high gauge face wear and GCC on the high rail, and plastic flow on the low rail, which appears as a periodic variation in vertical wear. This is illustrated by the measurements.
Damage of this severity is rare and usually results from excitation of a lateral resonance of the vehicle. This dynamic behaviour is usually “triggered” by variations in lateral track geometry e.g. poorly finished welds or joints. Sometimes a feature as simple as a walkway across the track or a level crossing is a sufficient “trigger”.
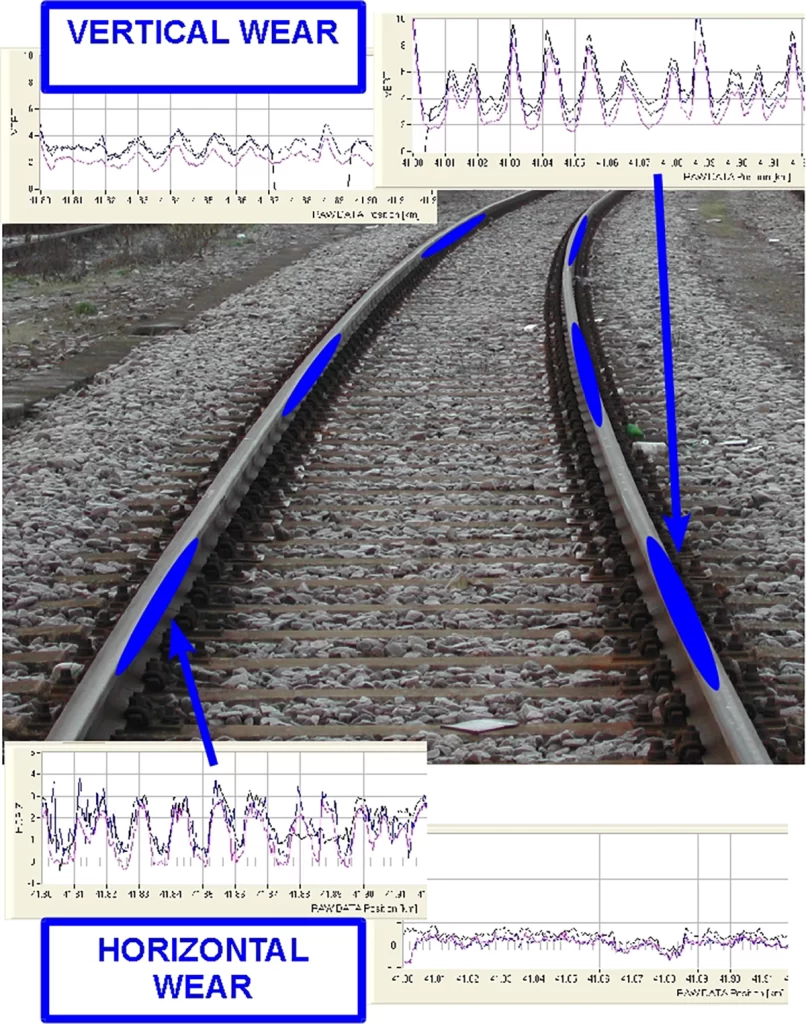
GCC sometimes appears periodically in so-called “clusters” as a result of a similar mechanism. “Clusters” of GCC are a feature primarily of large radius curves, but occur also in straights. In tighter curves GCC is usually either continuous or absent.
The best way to avoid periodic damage of this type is to maintain good lateral geometry, thereby eliminating the “triggers” for dynamic excitation. Because vehicles respond differently to lateral irregularities, problems may exist on one railway with one set of rolling stock that does not exist on an almost identical railway with different rolling stock.
Corrugation and related damage
The most common form of periodic damage on rails is corrugation. A well accepted mechanism for corrugation formation is shown.
The “wavelength-fixing mechanism” (WFM) is the dynamic behaviour that “fixes” both the wavelength and the position of corrugation along the track.
All types of corrugation whose cause has been identified to date are “constant frequency” phenomena, whose wavelength is λ = v/f where v = predominant train speed and f = frequency of the WFM.
WFMs that have been identified to date lie in the range of about 50-1200Hz. Examples of corrugation that occur from the following WFMs are considered here, in order of approximately increasing frequency:
Type of corrugation (WFM) | Approximate frequency (Hz) |
P2 resonance | 50-100Hz |
Rutting | 80-110Hz |
Trackform-specific | 150-350Hz |
Pinned-pinned resonance | 450-1200 Hz |
The “damage mechanism” causes the dynamic load (vertical or tangential) to result in an irregularity. The most common damage mechanism is wear.A basic classification of corrugation is given here by considering different WFMs. Because irregularities on a rail excite the dynamic behaviour, all corrugation can be reduced to some extent by ensuring a good longitudinal profile i.e. a “smooth” rail. Practical limits on irregularities left by typical reprofiling operations are proposed in a European standard1.
1 Railway applications – track – Acceptance of work – Part 3, Acceptance of rail grinding, milling and planing work in track, European Standard, EN 13231-3, European Committee for Standardisation, rue de Stassart 36, B-1050 Brussels, May 2006
“P2 resonance” corrugation
The so-called “P2 resonance” of the vehicle’s unsprung mass bouncing on the track stiffness is a common wavelength-fixing mechanism on all types of track, from trams to heavy haul railways. The examples shown are for a tram track in the street, a mass transit system, a freight railway, and a mixed passenger and freight line. Wear is the “damage mechanism” for the first two of these and plastic deformation for the others.
P2 resonance corrugation is a problem for metros in particular because it gives rise to low frequency “rumble” that is transmitted well into buildings. For conventional railways the wavelength of the resulting corrugation is usually at least several hundred millimetres, making the corrugation difficult to see.
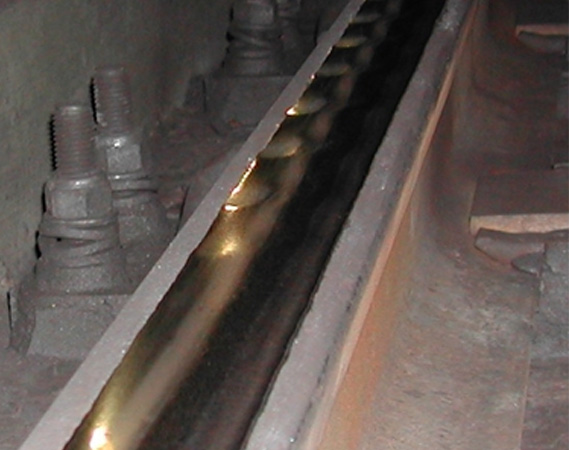
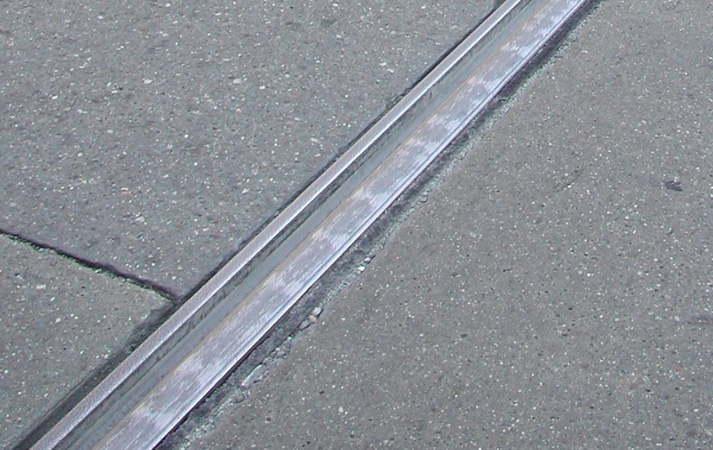
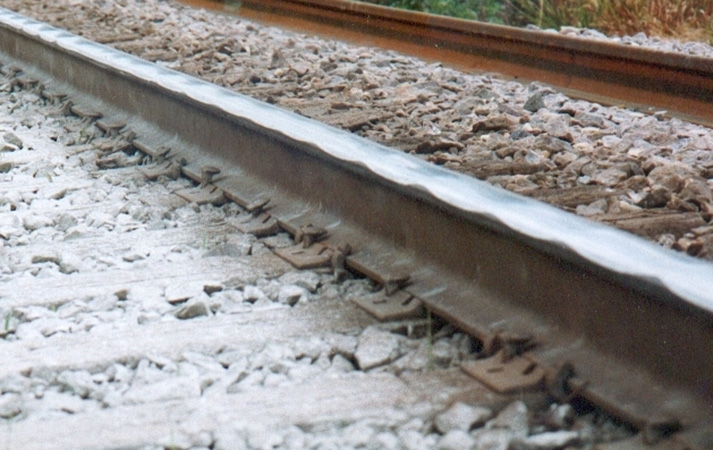
Low rail corrugation on the mixed passenger and freight line shown has occurred because the line is canted to suit passenger trains, and over-canted for the very much slower freight trains. Bogies steer badly in these conditions, giving very high tangential loading on the low rail. This causes quasi-continuous plastic flow, on which corrugation is superposed.
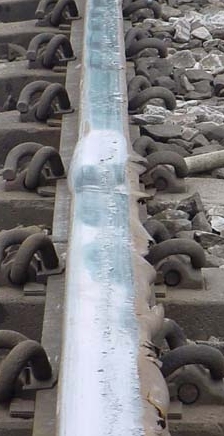
P2 resonance corrugation on non-ballasted track can usually be avoided using a sufficiently resilient, well-designed trackform.
A proven treatment of corrugation is to use harder rails as these reduce damage by both plastic flow and wear. Reprofiling should be undertaken routinely to retain an appropriate transverse profile that does not cause high stresses and RCF damage, and to minimise irregularities that “trigger” dynamic behaviour. An occasional damage mechanism is yield of the rail in flexure. When this is the case the corrugation can be avoided using rail with higher flexural rigidity and strength. Dynamic loads are usually critical, so irregularities should be minimised.
“Rutting”
“Rutting” occurs mainly on the low rail in curves. It results from excitation of a flexural resonance of a wheelset, excited by high lateral tangential forces. Wear is very periodic and often occurs rapidly. Rutting is exacerbated by applied traction and by high angles of attack of bogies.
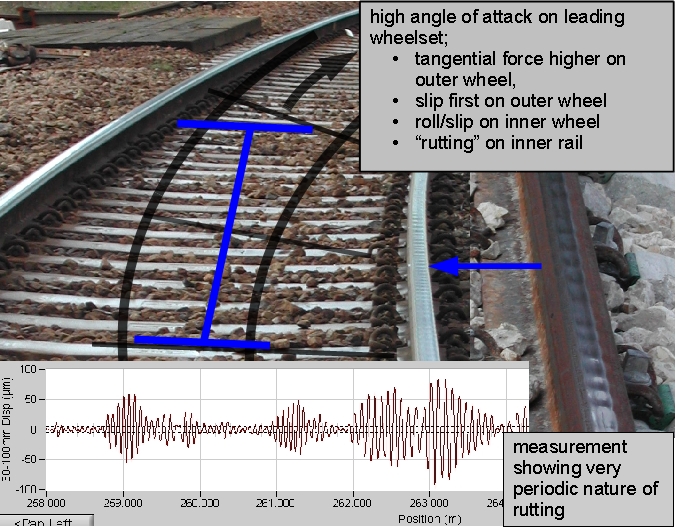
In existing track rutting can be reduced
- by reducing cant, thereby reducing the tangential force required for bogies to steer;
- by reprofiling to help steering;
- by controlling friction at the wheel/rail interface to reduce conditions for stick/slip.
Since rutting is a so-called “self-excited oscillation”, longitudinal irregularities are triggers but are not fundamentally important.
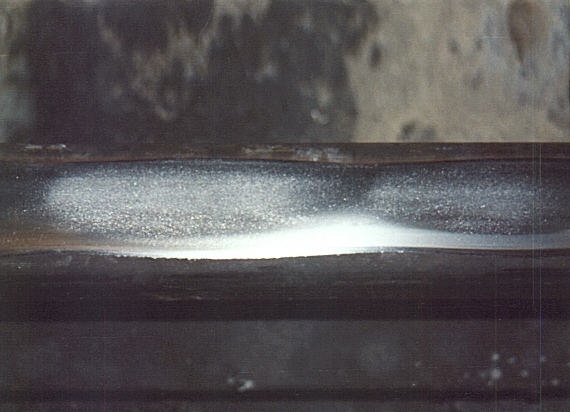
Trackform specific corrugation
Some trackforms have pronounced resonances that act as unusual wavelength-fixing mechanisms. An example is shown of corrugation in the 30-100mm wavelength range that has occurred on the low rail in a curve. On one trackform, between about 8.88km and 9.09km, there is severe and very periodic corrugation whereas there is minimal corrugation on the other trackform.
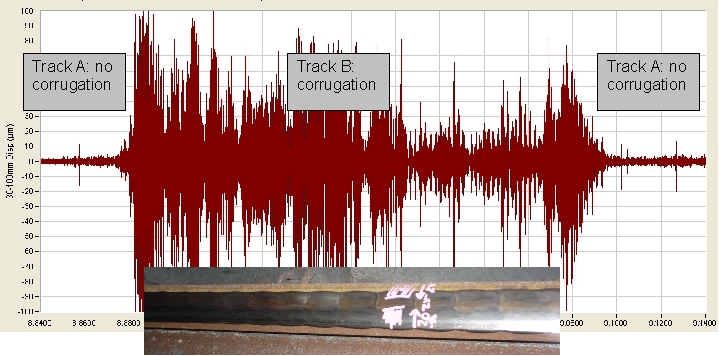
Pinned-pinned resonance corrugation
“Pinned-pinned resonance” corrugation arises from excitation of a resonance of the rail in which it vibrates as a beam with nodes almost at the sleepers. Examples are shown of this type of corrugation on ballasted track and on a metro, where there is a mix of both pinned-pinned resonance and P2 resonance corrugation. This type of corrugation occurs primarily on straight track and on the high rail in curves. High dynamic loads result from the dynamically stiff support, so corrugation is often worse on the approach to sleepers than at the more flexible mid-span position, where dynamic loads are lower.
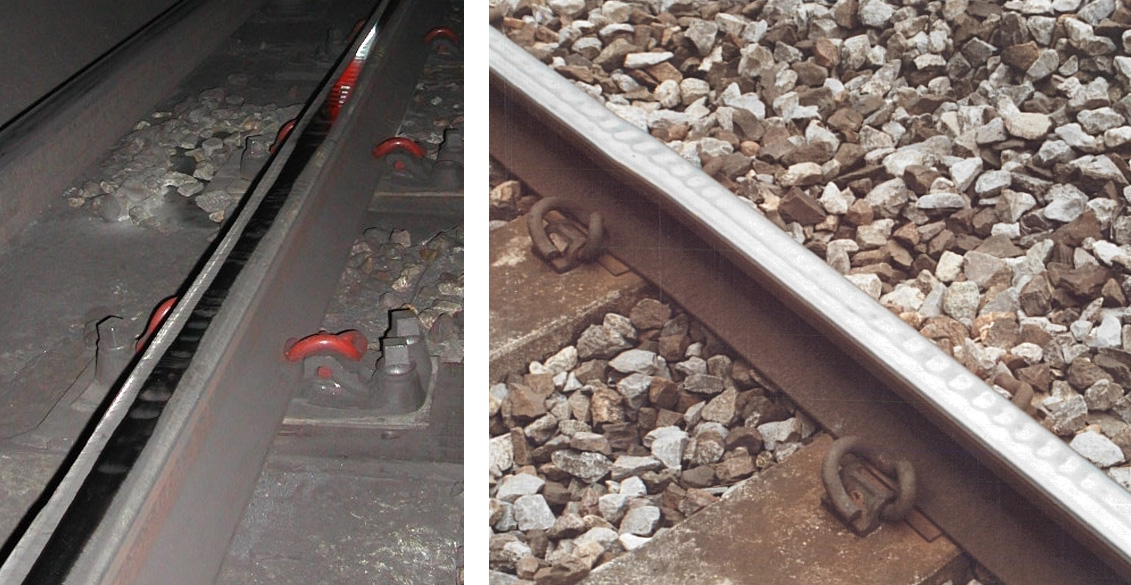
Pinned-pinned resonance corrugation is often associated with a loud “roaring” noise inside and outside the train (thereby giving rise to the term “roaring rails”). The pinned-pinned resonance has the highest frequency of common wavelength-fixing mechanisms.
“Belgrospis”
“Belgrospis” are not corrugation, but clusters of cracks, which appear on the peak of pinned-pinned resonance corrugation (20-100mm wavelength), between the rail centre and the gauge corner. To date they have been recorded only on sections of the German high-speed network.
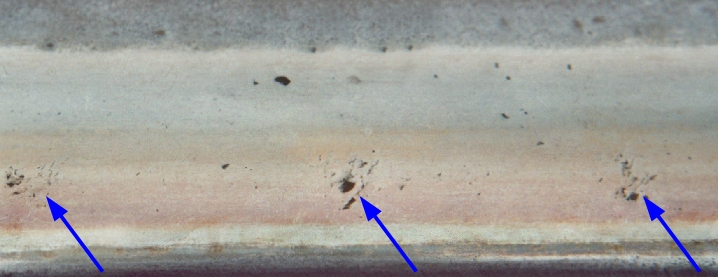