In this section:
Discrete defects
The most significant discrete defects are caused by rolling contact fatigue (RCF) and thermal effects.
Squats
Squats are RCF defects that occur in straight or gently curved track. They occur within the running band on the rail crown where the rail is heavily sheared from locomotive traction. Squats are sometimes known as “black spots”, where the dark area is a depression in the rail above the crack.
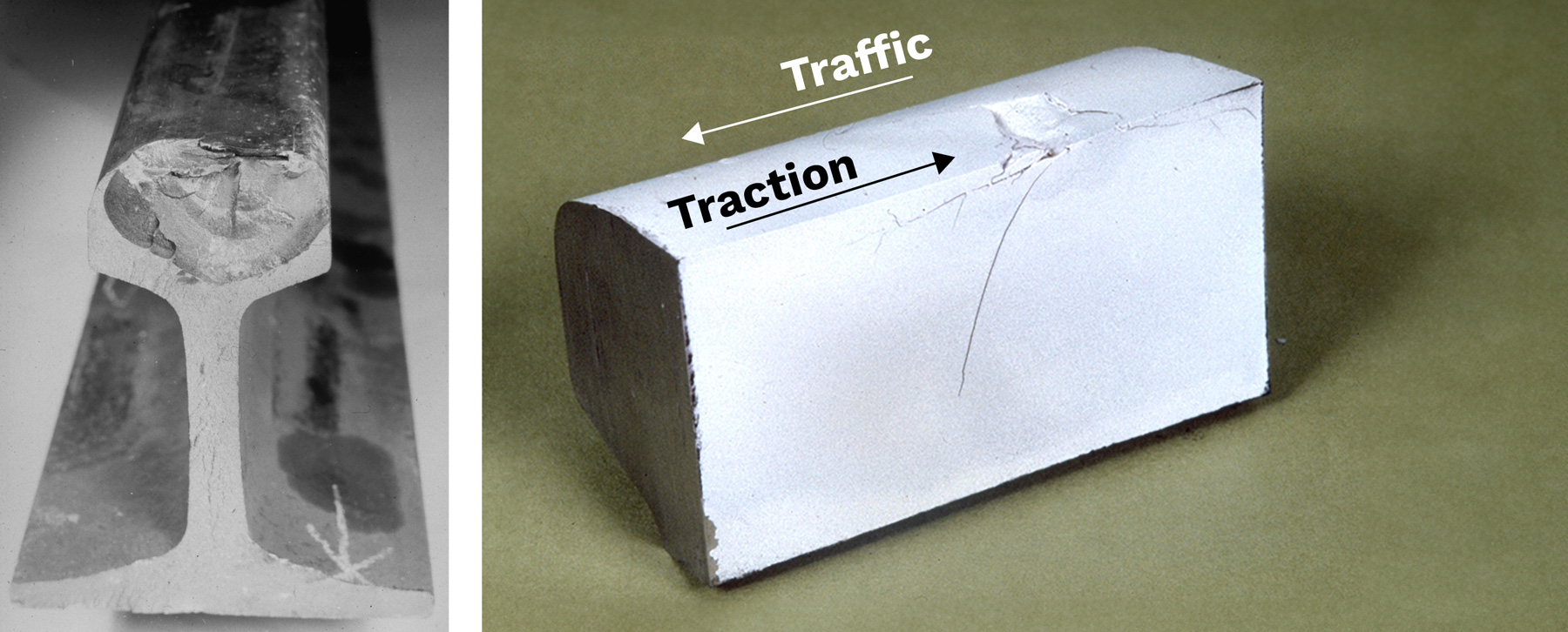
Squats are thought to initiate where small bits of hard material are trapped at the wheel/rail interface and cause one crack to grow rather than another. The direction of the crack can be felt, as with other types of RCF, by drawing a finger gently along the rail: the surface feels smooth when running a finger in the direction of traction but “ragged” in the opposite direction. The crack develops in the direction of the heavily sheared surface layer.
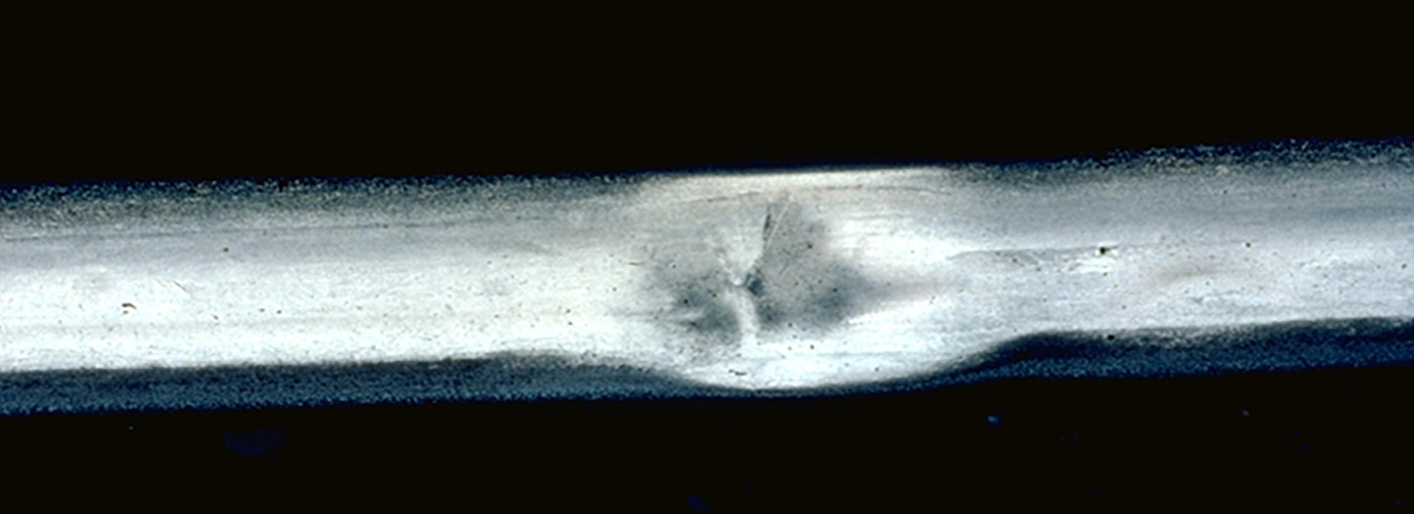
Essentially the same mechanism causes development of squats and GCC (Section 1.2). Transverse defects often result from squats that are left in track. Squats remain superficial in the absence of water.
Shells
Shells are RCF defects that initiate several millimetres under the gauge corner of the high rail. A close relationship has been found between the defect rate from shells and a shell index (the so-called “Clayton number”) — where the Sugino Index, SI, represents the length of oxide stringers:
A fatigue crack propagates initially parallel to the rail just under the gauge corner, then turns down into the rail to form a transverse defect (TD). The TD appears similar to that which occurs from a squat or from GCC.
The cleanliness of rail steel is now controlled deliberately to limit shells. Routine reprofiling is an important treatment for both squats and shells.
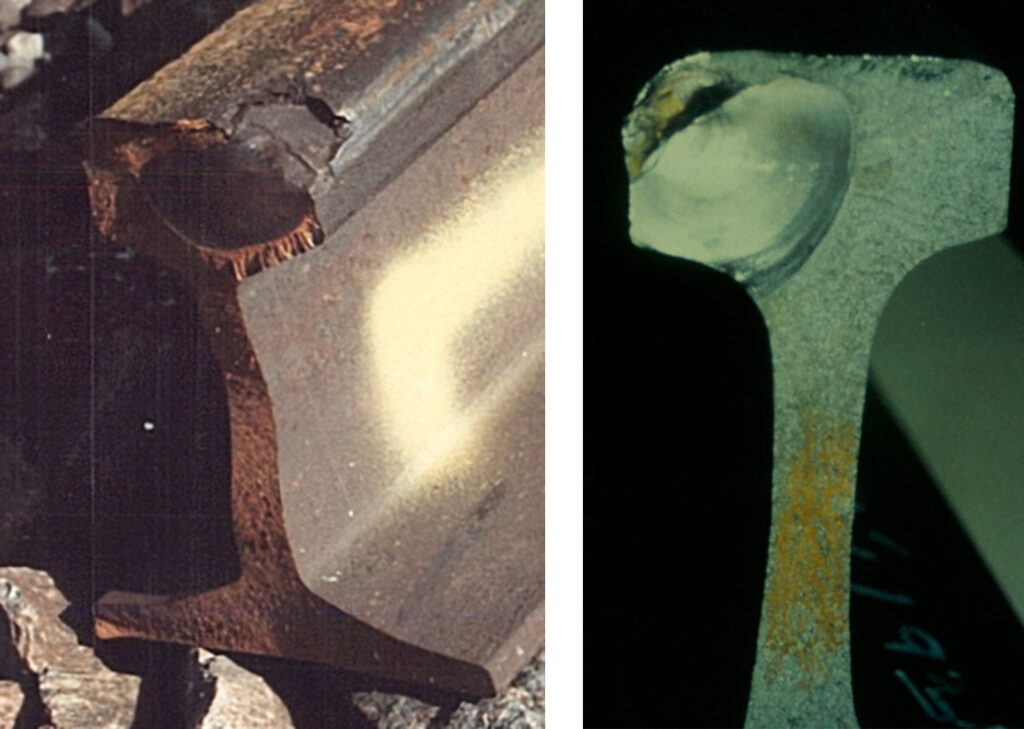
Wheelburns
Wheelburns occur where a wheelset has spun with little or no forward movement of the train. Concentrated heat input combined with rapid quenching from the body of the rail leads to localised thermal transformation. Transformation to martensite may occur, giving rise to brittle particles that are readily detached. Significant irregularities exist opposite one another on both rails. Thermal damage causes both surface and sub-surface cracking.

Whereas cracks resulting from RCF are quite uniform, those caused by thermal damage are more random.
Studs
Studs appear superficially very similar to squats: in particular they have two characteristic indentations in the rail surface. Although their cause is not yet well understood, cross-sections and circumstantial evidence suggest that they may initiate from thermal damage. They are associated mainly with areas of high traction demand and where friction differs on the two rails e.g. in curves rather than straight track. They do not occur in areas of sustained high friction, particularly in dry tunnels.
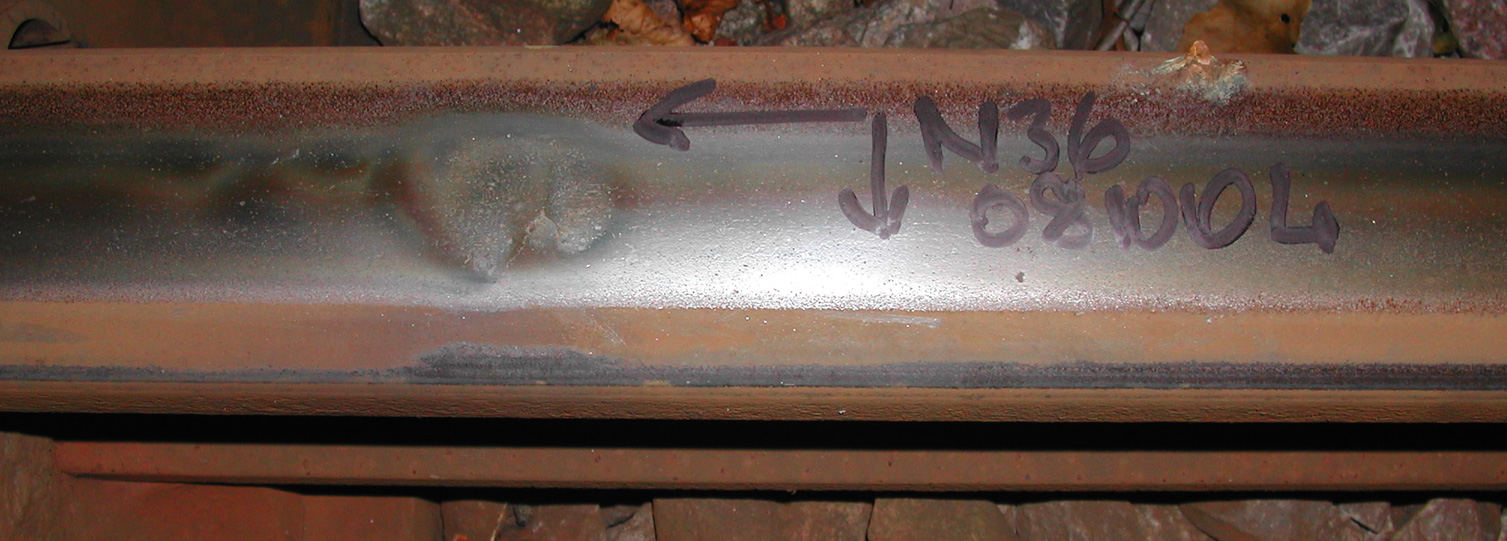
Studs usually occur on only one rail, although they can appear, often with different severity, opposite one another (when it may be difficult to differentiate them from a wheelburn). Sometimes the stud initiates corrugation, as shown here. Multiple studs are common. There is some association between studs and changes in rolling stock, particularly from DC to AC traction.
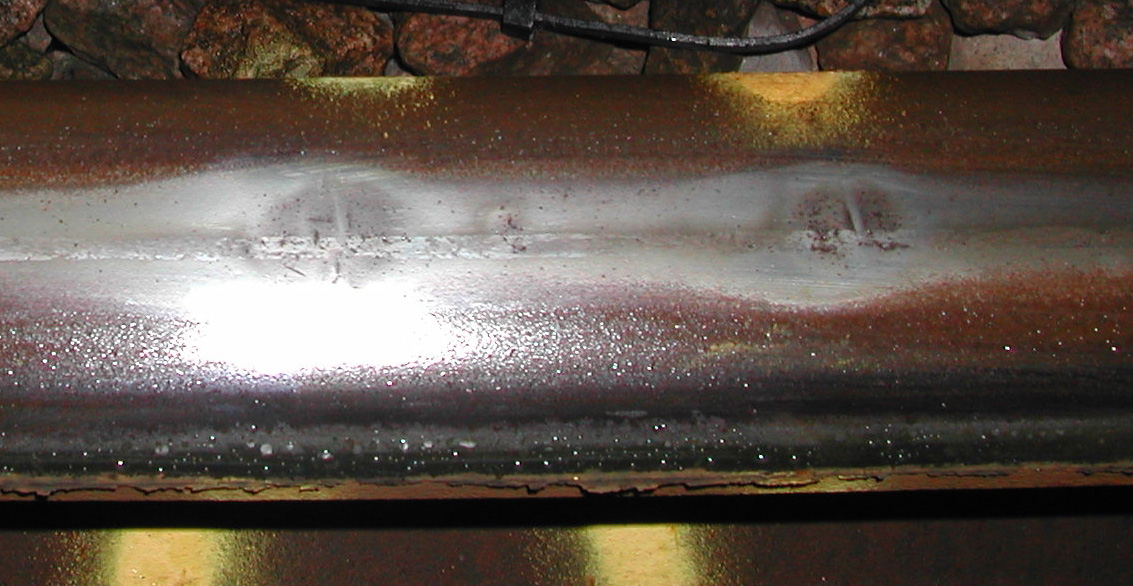
A cross section through a stud shows that there are sub-surface cracks, with a longer crack below the “running off” end of the crack mouth. These cracks cause the surface irregularities, with the larger irregularity above the longer crack. Although there are similarities with RCF, there are also significant differences.
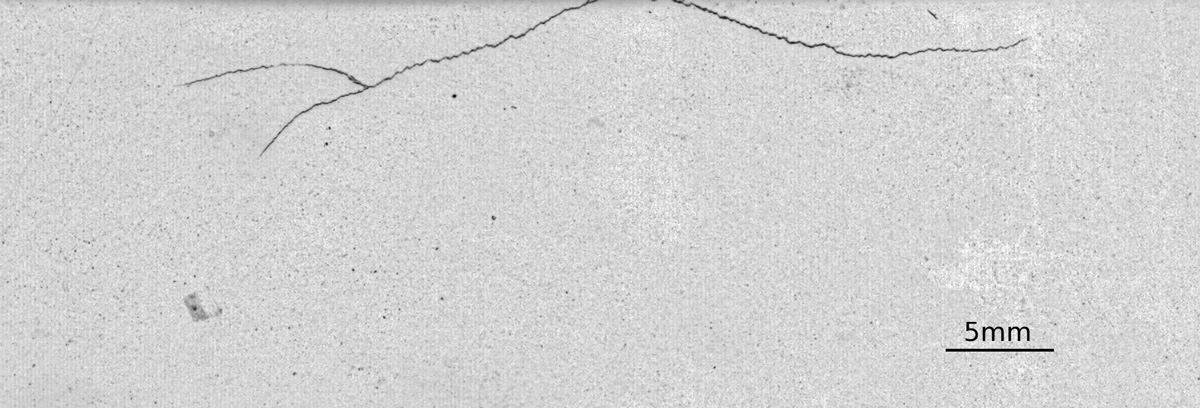
Squats, shells, wheelburns and studs represent significant irregularities on the running surface of the rail, which result in high impact loading. They are also a source of transverse cracks, as a result of which ultrasonic inspection of the rail may be impossible. Consequently, these defects should be removed, by localised grinding (which is possible only for the shallowest of defects), repair welding or rerailing. Routine grinding offers a viable preventative maintenance technique for most of these types of defects.
Isolated white etching layer (WEL)
Isolated patches of white phase or WEL can occur if wheelslip has been insufficient to cause a wheelburn or stud. These may appear opposite one another on both rails. At present it is not known if these are the origin of a more substantial defect, such as a stud, but they do represent a measurable irregularity.
Discontinuous patches of WEL are often the first sign of corrugation.
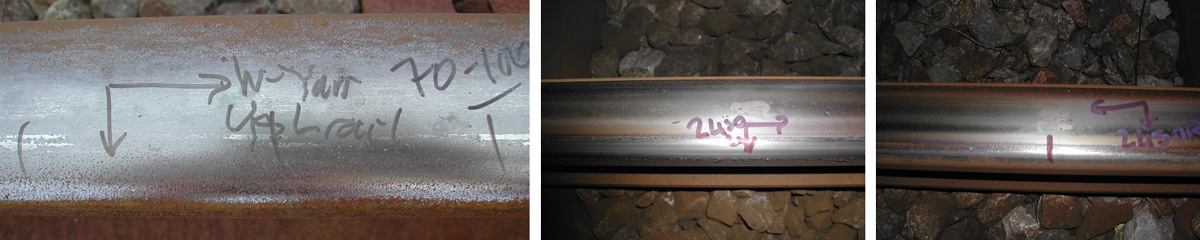
Plastic flow: Rail end batter
In jointed track there is an irregularity as a result not only of the joint itself but also of the relatively low stiffness of the bolted joint. This irregularity gives rise to high dynamic loading. Material also flows more readily because of the poor constraint of each rail end by the adjoining rail. Rail end batter is the result of high loads and poor constraint. This condition is best rectified by welding the rails to a satisfactory standard.
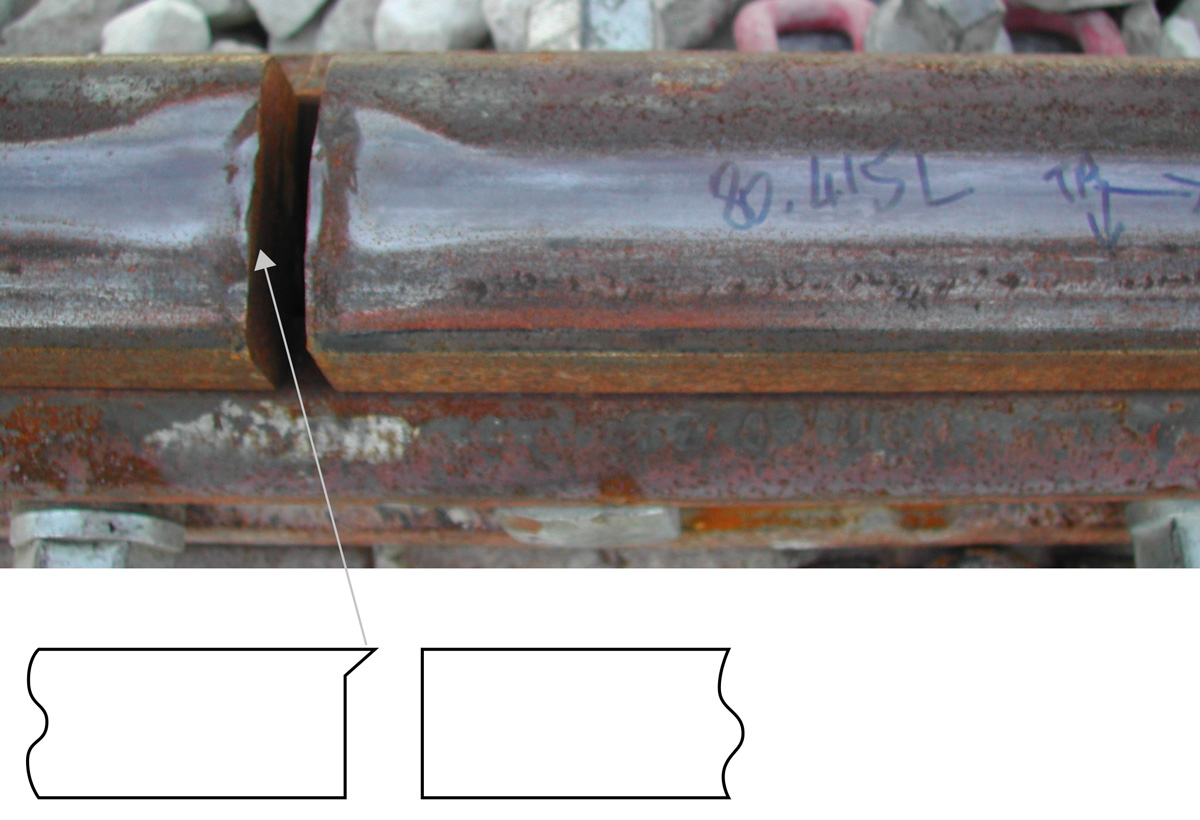
Spalling
Spalling is regarded here as detachment of macroscopic particles from the rail surface for whatever reason. Spalls may be isolated or there may be several in the same area.
Spalling associated with RCF
When RCF is initiated at the rail surface e.g. GCC, cracks can develop several millimetres into the rail if a fluid such as water or a lubricant is present. When cracks reach a depth that is approximately that of the so-called “compressive residual stresses” (typically about 5mm), they tend to go in one direction or another i.e. they “branch”.
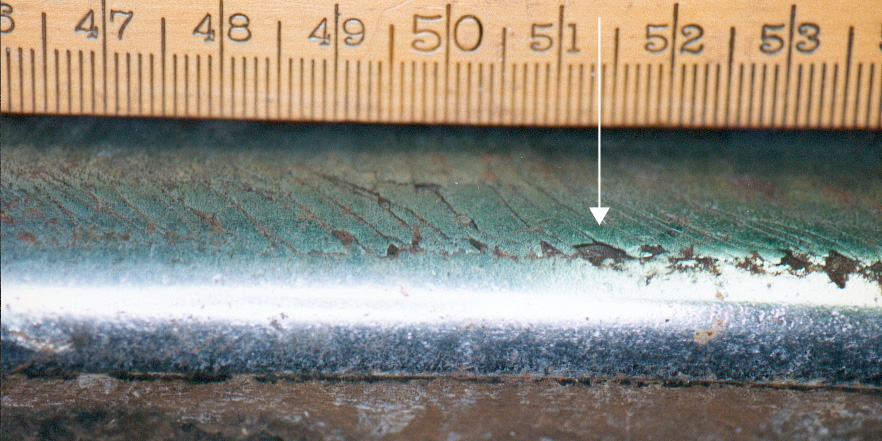
If a crack branches approximately parallel to the rail surface, it tends to meet up with another crack to form a spall. The crack is then no longer active and the spall is sometimes worn away by traffic.
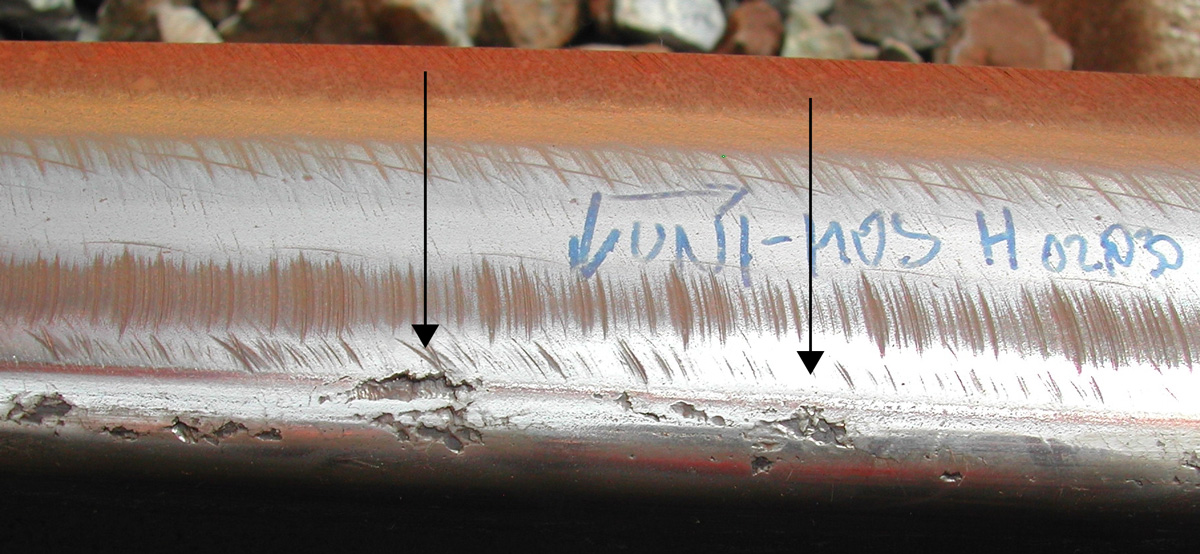
The conditions in which a crack branches parallel to the rail surface and those in which it branches down into the rail (potentially to form a transverse defect) are not yet fully understood.
There is some evidence that grease exacerbates spalling.
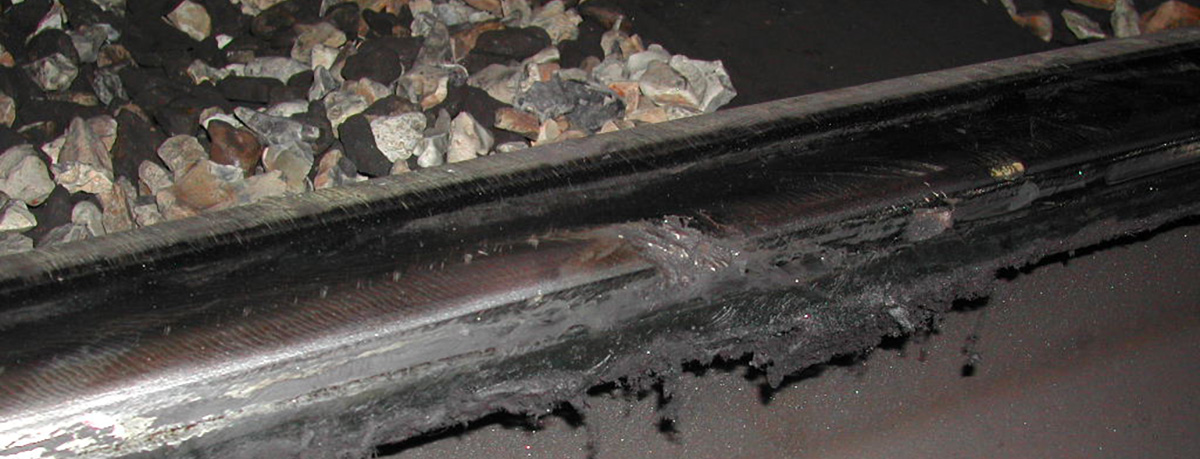
Spalling associated with plastic flow
Plastic flow results from high contact stress normal and tangential to the wheel/rail contact. In extreme cases flow gives rise to debris that spalls from the rail surface. This condition is often seen on the low rail of curves in dry underground tunnels, where friction is extremely high.
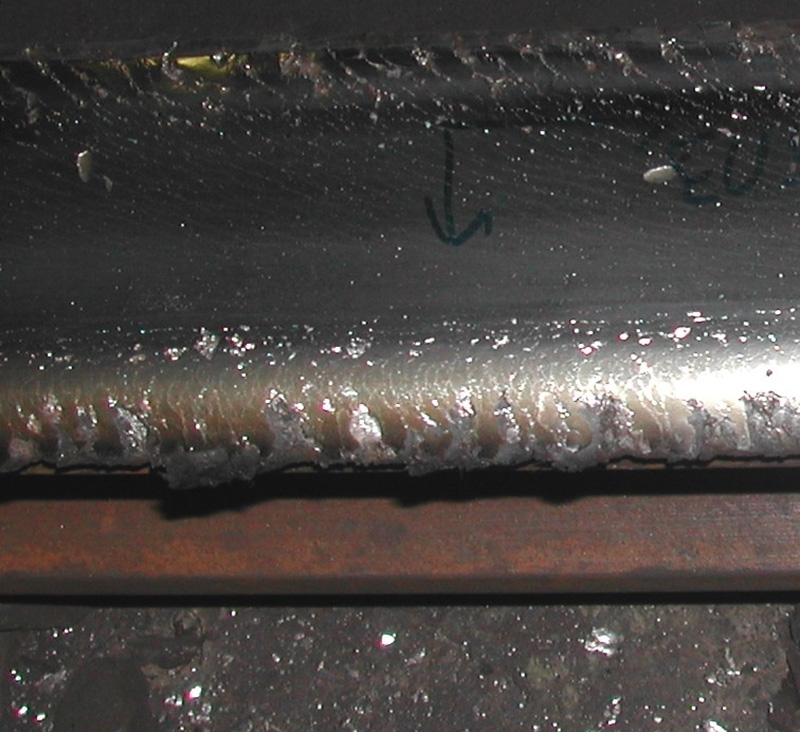
Spalling associated with thermal damage and wheelburns
The heat input to the rail from a spinning wheel usually gives rise to martensitic white phase (WEL) at the rail surface and also thermal cracking near the surface. Spalling occurs when the WEL becomes detached or the thermal cracks coalesce.
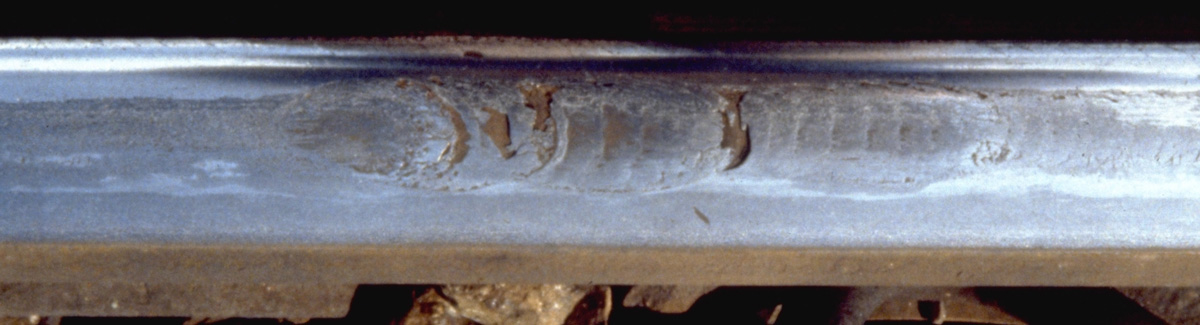
Ballast spalls
Ballast spalls occur when particles of ballast become trapped between wheel and rail. Usually these defects are relatively benign and wear out, but in some circumstances they can initiate squats or corrugation. Some damage of this type can be avoided by ensuring that ballast is brushed from the rails after reballasting of track, but ballast can sometimes be picked up by the slipstream of the train.
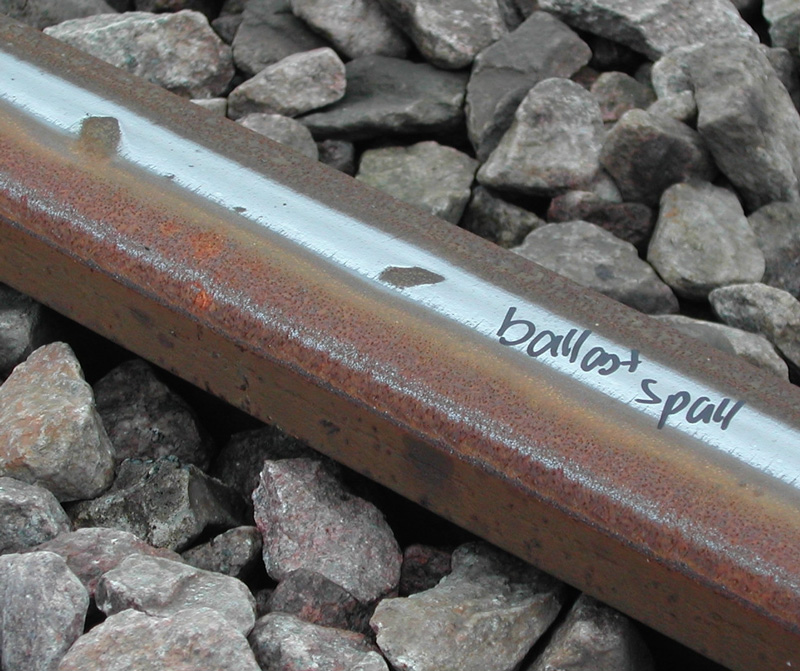